Rhodar creates huge enclosures for MOD Lyneham project
Posted on in Company News
Rhodar was commissioned by Amey Defence to undertake the removal of sprayed coating insulation residues and debris from within the large curved internal steel roofing structure of Hangar 209.
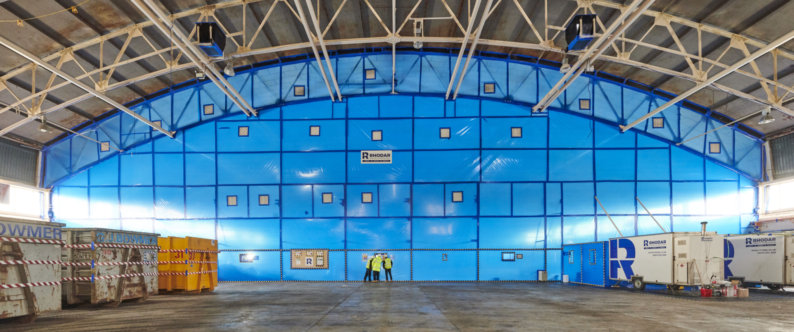
This enormous military structure (4,090m²), located at the MOD Lyneham facility, is due to be fully refurbished as a training facility for the base that will include the installation of new hangar doors.
This 12-week asbestos removal and cleaning project dealt with asbestos residues and debris left in-situ historically.
Pre-clean
Prior to the start of the main asbestos removal phase of the project, a comprehensive pre-clean of the entire floor area and all military equipment and vehicles within the hangar, under locally controlled conditions, was required.
The removal phase was then due to start immediately after the pre-clean, but this was delayed following the discovery by ecologists of protected barn owls nesting within the steel structure. A 6-month delay was then imposed to enable the breeding season to be completed.
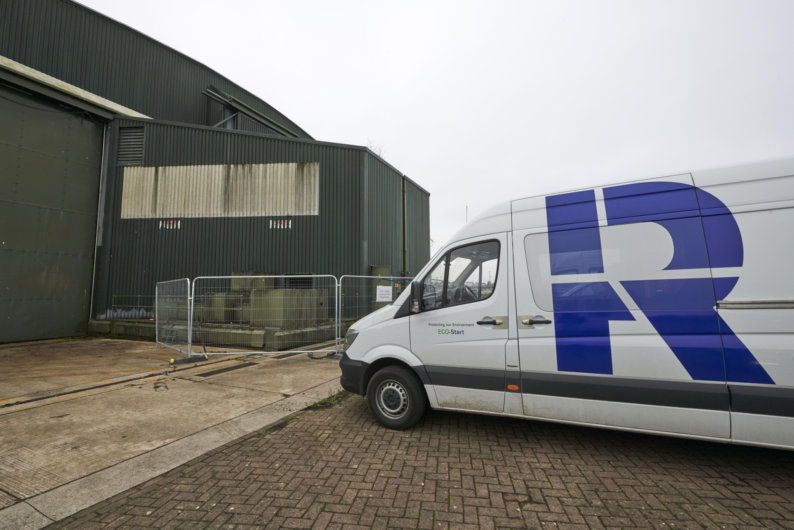
Enclosure construction
Following the all clear by the ecologists our site team of 14 security-vetted staff then began the complex process of constructing the large enclosure walls.
The sheer size and design of the hangar presented a number of challenges for our team, predominantly based around the curvature of the roof and height (15m at the highest point) necessitating the use of MEWPs to facilitate safe access.
Our IPAF operatives had to navigate precisely amongst the rafters of the intricate steel structures in order to gain adequate access to the work areas.
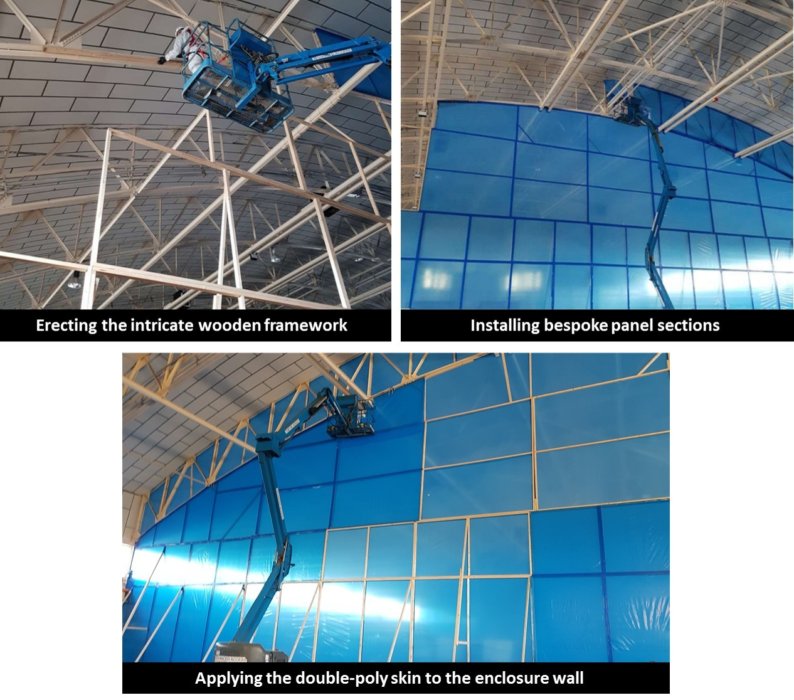
A high proportion of the double-skinned enclosure panels had to be bespoke-shaped to fit the curvature of the hangar, and as the panels were placed in position and built up we installed additional support struts to provide further structural integrity.

The vast size of the hangar, 90m long by 44m wide (with the apex up to 15m tall) meant that we broke the removal process down into 3 equally-spaced, sequential zones and adopted a 180-degree flip approach to re-use one in-situ enclosure wall structure for each zone – saving time and materials.
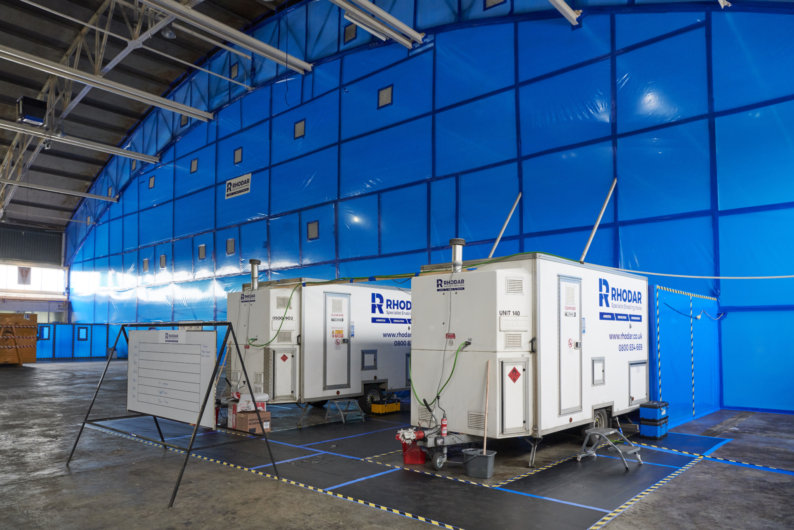
Creating the required negative pressure
Each enclosure consisted of two bespoke-panelled walls and the vast cubic area required in excess of 184,800cmh of negative pressure to be generated. To produce this we utilised a total of 27 Negative Pressure Units, comprising of both 5,000 and 10,000cmh units and to ensure adequate air management we affixed up to 20 intake filters to designated areas of the opposite enclosure wall.
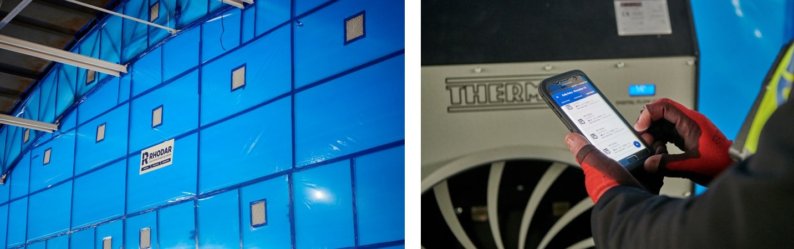
As well as establishing external bowsers for fuel and water, another key part of the set-up on site was the installation of a bespoke electrical distribution board to manage the level of power required for this number of NPUs. This also included the use of high capacity electrical cabling throughout.
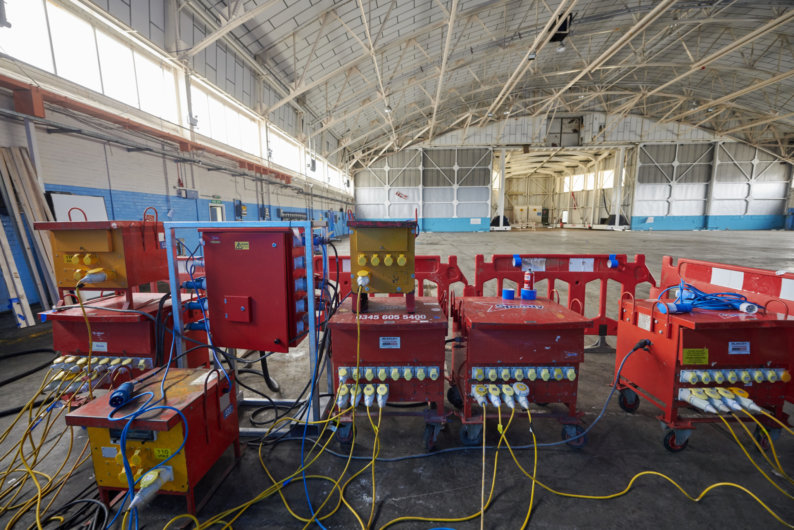
The Removal Process
In order to facilitate the fine cleaning of the steel roof the team first had to remove a primary ceiling structure that contained over 5,000 non-asbestos MMMF ceiling tiles (sized 1200mm x 600mm), MMMF quilt insulation & associated metal tracking and supports that were affixed to the roof.
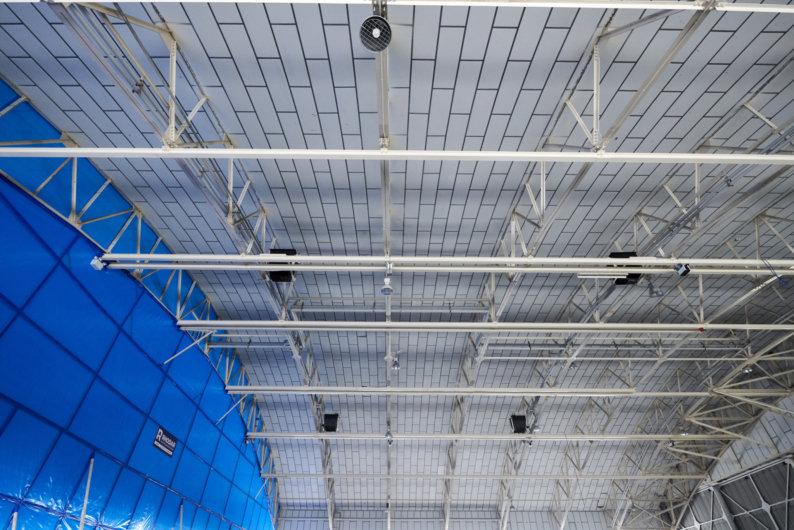
They conducted this via a systematic movement across the ceiling to remove all tiles in an entire zone in conjunction with low pressure dust suppression spraying. This involved each tile being removed and then packed into special oversized asbestos bags.
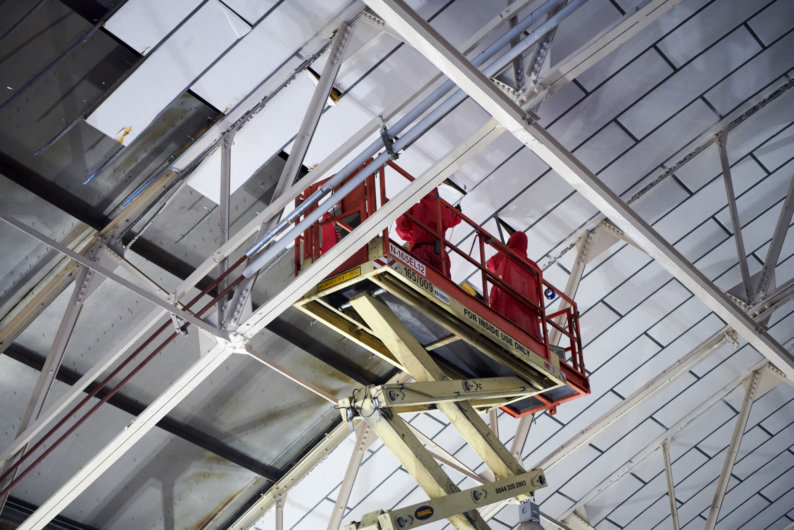
Following this the asbestos removal and cleaning process to the steelwork could then begin – this consisted of manual scraping and bagging whilst spraying and shadow vacuuming in a reverse direction back across the ceiling area.
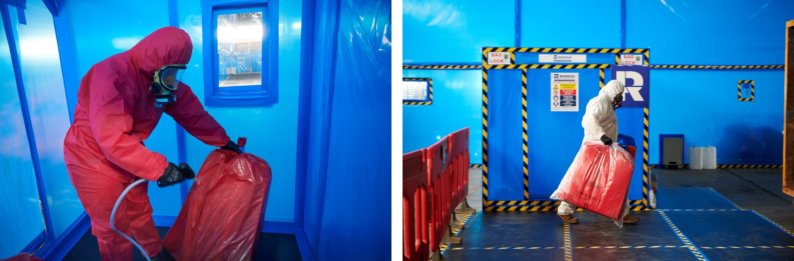
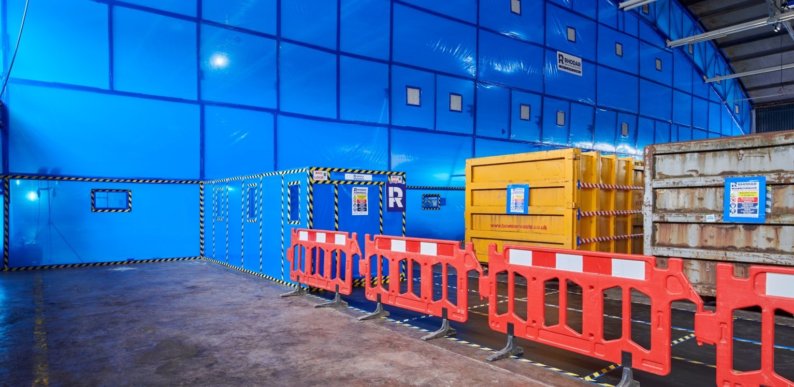
Zone inspection
As each of the 3 zones was deemed to be complete Rhodar’s Site Supervisor conducted a visual inspection and once satisfied invited the onsite analyst to conduct a 4-stage clearance of the zone and to issue the certificate for reoccupation.
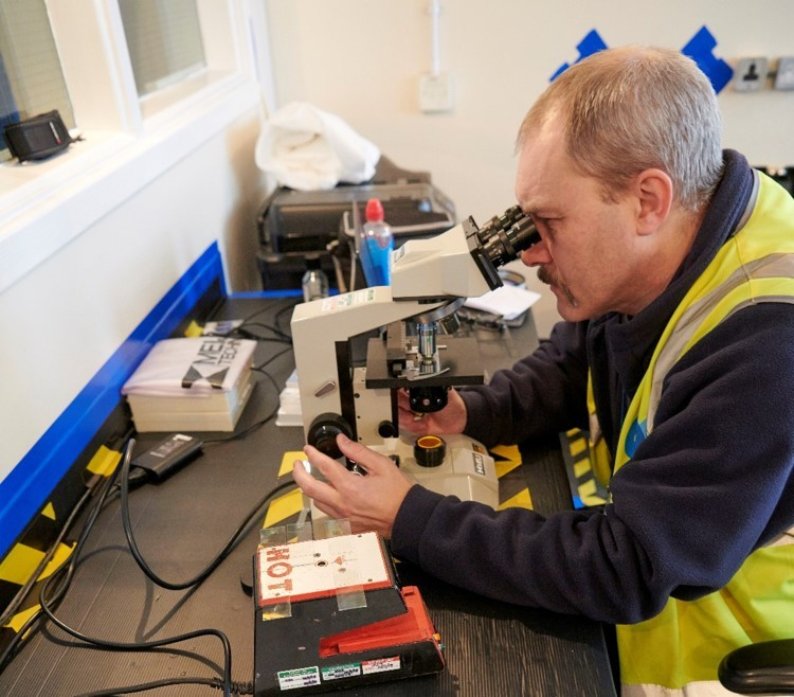
The analytical team was present throughout the project conducting background and personal monitoring on a daily basis along with subsequent 4-stage clearance testing.
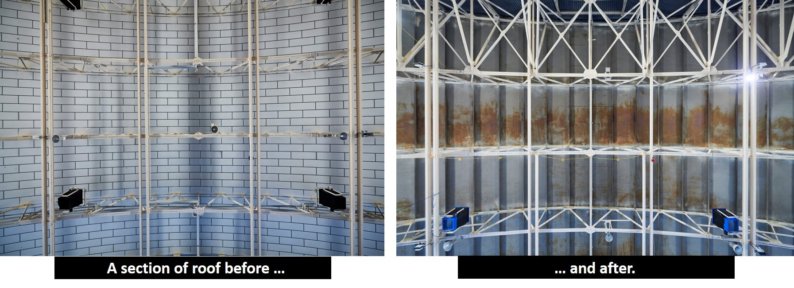